A evolução na jornada Lean: case Usaflex
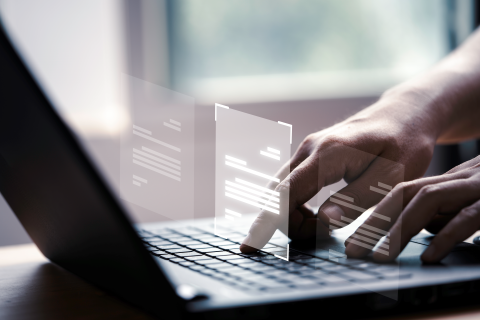
Por: Admin - 30 de Novembro de -0001
De uma maneira geral, as indústrias calçadistas possuem ainda muito enraizados os conceitos do Sistema de Produção em Massa – visão Fordista – ligados ao seu histórico de grandes lotes e um mix reduzido para exportação (baixa variedade).
Embora a realidade desse segmento venha mudando para pequenos lotes e um aumento significativo da variedade de produtos e de customizações, estas empresas avançaram pouco em aprofundamento dos conhecimentos de Lean Manufacturing e gestão de processos por fluxos.
Neste vídeo, Marcelo Guimarães, diretor industrial na Usaflex, fabricante de calçados, explica como otimizou seu espaço físico e mão de obra, além de reduzir lead time e custos indiretos a partir dos conceitos e técnicas do Lean Manufacturing.
O vídeo foi extraído do evento on-line "A evolução na jornada Lean – caso Usaflex" que traz, além da implantação do Lean Manufacturing na empresa Usaflex, um debate com Marcelo Guimarães, diretor industrial na Usaflex, Jácome Cruz, sócio-consultor da Produttare, e Junico Antunes, CEO do Grupo Produttare. Clique aqui para assistir ao webinar na íntegra.
A Usaflex
Fundada em 1998, a Usaflex é pioneira e líder nacional na fabricação de calçados de conforto e moda para mulheres de todas as idades. Em 2016, passou a ser gerida por um fundo de Private Equity, o que possibilitou uma maior capacidade de investimento e profissionalização da gestão.
A empresa possui quatro plantas industriais localizadas no Rio Grande do Sul e sua matriz está localizada em Igrejinha, sendo as demais unidades em Parobé, Campo Bom e Dois Irmãos, respectivamente.
Com cerca de 3 mil colaboradores e uma capacidade de produção de 5.500.000 pares de calçados por ano, seu grande diferencial competitivo é o conforto, sendo esse critério considerado em todas as tomadas de decisões. A Usaflex está presente em diversos canais como lojas multimarcas, franquias, exportação e e-commerce.
Contexto
A indústria calçadista no Brasil ainda possui forte influência de um paradigma Fordista, focado nos sistemas de produção em massa, baseado em um histórico de exportações, em que outros países compravam em grandes lotes, e em um mix reduzido (de baixa variedade).
Alicerçada nessa realidade, a indústria calçadista demorou a entender algumas mudanças que estavam ocorrendo no mercado, como o aumento constante da variedade e, consequentemente, a redução de tamanho dos lotes, a necessidade de flexibilização do processo de fabricação devido a esse mix maior e a customização. Tudo isso, aliado a necessidade de redução de custos de fabricação devido ao cenário altamente competitivo que se desenhava.
Frente a esses novos desafios, a Usaflex decidiu em 2017 iniciar o processo de implantação dos conceitos de Lean Manufacturing com o objetivo de aumentar a produtividade, reduzir seu lead time, melhorar o aproveitamento das instalações, reduzir estoque em processo (WIP) e reduzir mão de obra indireta.
Para isso, buscou a Produttare para auxiliar na jornada Lean. Inicialmente foi criado um Road Map para suportar o planejamento da jornada e garantir o sucesso da implantação dos conceitos.
A partir do Road Map foram divididas as necessidades de implantação da jornada Lean em cinco projetos:
- Adequação de uma linha: neste projeto foi escolhido uma parte do processo para implantação dos conceitos e adequações;
- Família de Produto x Planta Industrial: consiste no estudo de adequações de famílias de produto de acordo com as suas características e vocação das plantas;
- Adequação de uma planta: de maior porte, este projeto envolveu adequações e implantação de conceitos e mudança de layout em uma das plantas da empresa;
- Capacitação: ocorreram diversos treinamentos focalizados ao longo dos projetos, mas também houve uma capacitação em Lean, estruturada em atividades didáticas em sala e na fábrica, mesclando teoria e prática;
- Redução da Não Qualidade: previsto para iniciar em março de 2020, foi interrompido devido à pandemia do Covid-19, com previsão de início em 2021.
Projeto 01: Adequação de uma linha
O primeiro projeto teve início no final de 2017 e durou 5 meses. Nele foi definido que apenas uma das fábricas de montagem seria o foco para implantação dos conceitos, técnicas e métodos do Lean Manufacturing.
Após o treinamento inicial da equipe de trabalho, constituída por cerca de 20 pessoas de diversas áreas da empresa, foi realizado o mapeamento do fluxo de valor, a partir Value Stream Mapping (VSM), além de um mapeamento adicional no modelo do Shigeo Shingo – o Mapa do Fluxo de Processo (MFP).
Identificando as perdas na Função Processo e na Função Operação, foram encontradas várias oportunidades de melhorias, que possibilitaram a construção de um conjunto de indicadores a partir do Mapa do Estado Atual , os quais serviram como referência para o desenho do Estado Futuro.
Todo projeto foi baseado em eventos kaizens de uma semana com equipes multifuncionais dedicadas. A partir destes kaizens foi elaborado um Mapa do Estado Futuro, dando-se início às implantações das melhorias propostas, fundamentalmente às alterações práticas de layout, que passou de um layout departamental (posicional) para um layout em fluxo, visando o fluxo contínuo dos itens produzidos.
Entre os resultados obtidos ressalta-se a redução do lead time de 4 para 2 dias, redução de 50% do estoque em processo, redução de 10% da mão de obra indireta, melhoria nos índices de qualidade, além da capacitação da equipe, a disseminação da cultura da produção enxuta e a multifuncionalidade.
Projeto 02: Família de Produto x Planta Industrial
Este projeto foi realizado no final de 2018 com duração de 3 meses, sendo mais teórico e focado nas áreas de engenharia de produto, engenharia de processos e PPCP (Planejamento, Programação e Controle da Produção).
Trabalhou-se formação de famílias de produtos a partir de suas semelhanças de processos, observando-se a vocação operacional das plantas existentes, e direcionando as diferentes famílias em diferentes plantas industriais, de forma que cada planta inicie o processo de fabricação a partir das matérias primas e entregue ao final do fluxo, um produto acabado, pronto para a Expedição. Este projeto permitiu identificar a planta piloto para implantação em maior profundidade, dos conceitos Lean, que seria o projeto 03.
Todos os modelos de calçados foram classificados como de Simples, Média ou Complexa construção e foram agrupados de acordo com as quatro plantas de fabricação, considerando as particularidades de cada uma.
Os resultados deste projeto foram:
- Identificação das variáveis que impactam na complexidade da produção;
- Compreensão do impacto da tecnologia na produção para os diferentes modelos;
- Maior entendimento da alocação de determinados modelos em plantas com arranjo físico facilitador e com tecnologia mais adequada;
- Melhor alocação das equipes de produção em função da complexidade de produção.
Projeto 03: Adequação de uma planta
Para uma implantação mais aprofundada dos conceitos do Lean Manufacturing em uma planta, foi definida a unidade de Parobé como piloto. O projeto iniciou em 2019 e durou cerca de 8 meses.
Este projeto teve como objetivo melhorar o aproveitamento do espaço físico, colocando duas linhas de produção completas no mesmo ambiente físico, reduzindo o lead time e a mão de obra indireta bem como aumentando assim a eficiência produtiva.
Para a implantação foram realizados quatro kaizens: (i) 1º Kaizen com foco no desenho do macro layout; (ii) 2º Kaizen para a finalização do macro layout e definição e posicionamento dos Buffers; (iii) 3º Kaizen para dimensionamento dos Buffers e desenho das Rotas Logísticas de abastecimento dos fluxos; (iv) 4º Kaizen para o desenho dos indicadores e fluxo de programação. Para dar subsídios aos kaizens foi realizado o mapeamento do fluxo, estudo de layout, de capacidade e de lógica de programação.
Os principais resultados foram o aumento da produção de 1.800 pares para 3.600 pares por dia, além da redução de estoque em processo e de 25% do lead time e simplificação de sequenciamento.
Projeto 04: Capacitação
Neste projeto foi realizado uma capacitação para 32 colaboradores da empresa Usaflex, que contou com 96 horas de teoria (horas/aula) e 24 horas de trabalhos práticos na produção ao final de cada módulo, tornando possível a aplicação prática dos conceitos aprendidos em sala.
Resultados Gerais da Jornada Lean Manufacturing
Embora para a Usaflex a jornada do Lean Manufacturing esteja no início, alguns resultados quantitativos já são visíveis como:
- Redução do lead time tanto no projeto piloto quanto na planta de Parobé;
- Redução de MO indireta;
- Redução de falhas por não qualidade;
- Aumento de produtividade;
- Otimização dos fluxos;
- Redução de estoques;
- Simplificação do fluxo de programação.
Outros resultados qualitativos que auxiliam para manter os conceitos a jornada Lean são:
- Disseminação da cultura Lean Manufacturing na organização;
- Capacitação do quadro de colaboradores;
- Utilização de conceitos teóricos para obtenção de resultados práticos;
- Processo de melhoria contínua.