Análise crítica do inter-relacionamento das perdas e dos subsistemas do Sistema Toyota de produção
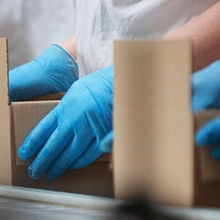
Por: Admin - 29 de Dezembro de 2014
Autores:
José Antonio Valle Antunes Júnior
Universidade do Vale do Rio dos Sinos – UNISINOS e PRODUTTARE Consultores Associados
Rua 24 de Outubro 111/1103, Moinhos de Vento 90510-002 – Porto Alegre - RS
Marcelo Klippel
Pontifícia Universidade Católica do Rio Grande do Sul - PUCRS e KLIPPEL Consultores Associados
Rua 24 de Outubro 111/1103, Moinhos de Vento 90510-002 – Porto Alegre - RS
Abstract
This paper presents a critical analysis of the subsystems that compose the Toyota Production System – TPS. These subsystems are derived from pillars of the TPS: the Competition Rules, the Production Function Mechanism and the Wastes in Production Systems. Also, the article presents the inter-relationships that exist between the subsystems and the wastes and also between the subsystems of the TPS. Finally, the article makes evident the need to understand in depth the TPS by this systemic inter-relationship between the various subsystems that compose it and the total elimination of wastes in the production systems.
Key Words: TPS, Wastes, Inter-relationships
1.) Introdução
O Sistema Toyota de Produção, também chamado de Sistemas de Produção Enxuto, constitui-se em uma importante ferramenta para o desenvolvimento da Competitividade Empresarial. Na verdade, pode-se analisar conceitualmente a construção do Sistema Toyota de Produção a partir de três fases inter-relacionadas a saber: i) Base Conceitual da Construção do Sistema Toyota de Produção; ii) O Sistema Toyota de Produção em si, constituido de diversos Subsistemas; e iii) As Técnicas de Operacionalização do Sistema Toyota de Produção. A Figura 1 abaixo mostra os aspectos básicos de análise e de construção gerais do Sistema Toyota de Produção.
A partir da Figura 1 pode-se perceber que o Sistema Toyota de Produção foi construído baseado em três pilares fundamentais: i) As Normas da Concorrência; ii) O Mecanismo da Função Produção; e iii) As Perdas nos Sistemas Produtivos (Antunes, 1998). A partir destes pilares foram gestados um conjunto de Subsistemas no intuito de colocar em prática os conceitos do Sistema Toyota de Produção.
No entanto, o esclarecimento de algumas relações torna-se importante para uma melhor compreensão do funcionamento teórico e prático do Sistema Toyota de Produção. O presente artigo pretende responder a duas questões essenciais, a saber:
Figura 1 - Aspectos Básicos de Análise e de Construção do Sistema Toyota de Produção
• Quais as inter-relações, ou seja, os graus de interação, entre os diversos Subsistemas que constituem o STP e as Perdas nos Sistemas Produtivos?
• Quais as inter-relações, ou seja, os graus de interação, existente entre os diversos Subsistemas que constituem o Sistema Toyota de Produção?
2.) As Perdas, as 7 Perdas e os Subsistemas do STP
A seguir é apresentado sucintamente os conceitos básicos de Perdas nos Sistemas Produtivos e os diferentes Subsistemas do Sistema Toyota de Produção.
Um detalhamento do conceito de Perdas foi proposto conjuntamente por Ohno (1997) e Shingo (1996a). Trata-se da noção de 7 Perdas. Estas Perdas são:
1. Perdas por superprodução (quantitativa e por antecipação): representam aquelas Perdas decorrentes da produção antecipada de produtos, imobilizando-se produtos finais antes do necessário ou devido à produção excessiva, nas quais se produz mais do que a demanda. Esta prática consome capacidade de produção dos recursos quando não são necessários ocasionando possíveis atrasos de outros produtos que não dispõem de capacidade. Geralmente, a superprodução tem por objetivo “compensar” a produção de produtos defeituosos ou fazer estoque. Em ambos os casos há o desperdício.
2. Perdas por transporte: a atividade de transporte é uma operação que não agrega valor ao produto uma vez que a forma do material não se altera desde o início até o fim do ciclo. Logo, busca-se a eliminação desta operação pela mudança do leiaute das instalações. Mecanizar idealmente um transporte, por exemplo, pode eventualmente melhorar a eficiência desta operação, mas no máximo ocasionará uma redução dos custos de transporte não representando em ganhos para o sistema como um todo.
3. Perdas no processamento em si: neste tipo de perda, inúmeras atividades podem ser realizadas sem que contribuam para a melhoria da qualidade do produto sendo desta forma desnecessárias. Neste caso, é preciso um trabalho de investigação pela agregação de valor para a identificação das mesmas e eliminação deste tipo de perdas.
4. Perdas devido à fabricação de produtos defeituosos: a fabricação de produtos defeituosos, que não atendam às especificações de qualidade projetadas, constitui um desperdício que aumenta os custos de produção. Para a sua eliminação deve-se realizar uma inspeção visando identificar e prevenir a ocorrência destes produtos. A simples identificação destes produtos não irá resolver o problema, uma vez que ele tenderá a se repetir. Deve-se atacar a causa e não a conseqüência.
5. Perdas nos estoques: um dos paradigmas derrubados pelo STP é o de que havia necessidade de formação de estoques no processo produtivo (estoque em processo) ou no almoxarifado/expedição (matéria-prima/produto acabado). O desenvolvimento do Just-in-Time comprovou que a existência de estoques na realidade apenas encobre imperfeições, constituindo-se em desperdício. A eliminação de estoques tanto no almoxarifado como nos produtos em fabricação deve ser perseguida.
6. Perdas no movimento: As perdas por movimento são aquelas relacionadas com os movimentos feitos pelos trabalhadores sem que estes sejam necessários.
7. Perdas por espera: a falta de balanceamento no processo de produção ocasiona a paralisação de postos de trabalho resultando em baixa taxa de ocupação de equipamentos e paralisação da atividade humana, caracterizando as perdas por espera. Elas podem ocorrer, também, quando ocorre o setup dos equipamentos. O estudo da redução deste, através da Troca Rápida de Ferramentas – TRF, tem por finalidade a redução deste tipo de perda.
Na seqüência, são apresentados de forma sucinta os diferentes Subsistemas que constituem o Sistema Toyota de Produção.
Os subsistemas do STP são os seguintes:
1. S1 - Subsistema de Quebra-Zero (MPT): o Subsistema de Quebra-Zero evidencia a importância da utilização da Manutenção Produtiva Total no corpo do Sistema Toyota de Produção e o pressuposto de sustentação é que: “o STP não poderia deixar de dispensar uma atenção especial às máquinas, pois os estoques mínimos entre processos não são suficientes para absorver paradas por quebras que afetariam a produção” e “o funcionamento de uma máquina ou equipamento em condições precárias aumentaria o risco da geração de produtos defeituosos, o que também afetaria o fluxo de produção” (Ghinatto, 1996, p.145).
2. S2 – Subsistema de Defeito-Zero (CQZD/Autonomação): conforme Taiichi Ohno, dois são os pilares de sustentação do Sistema Toyota de Produção: O Just-In-Time e a Autonomação (Automação com Toque Humano). Por outro lado, Shigeo Shingo desenvolveu um trabalho visando especificamente atacar o problema da garantia da qualidade dos produtos e dos processos que culminou na geração do conceito de Controle da Qualidade Zero-Defeitos - CQZD. Uma articulação conceitual e prática entre a Autonomação e o Controle da Qualidade Zero-Defeitos foi proposto por Ghinatto (1996). Ghinatto (1996) sustenta que o conceito de Controle da Qualidade Zero-Defeitos constitui-se em elemento básico para que seja possível atingir de forma plena o conceito de Autonomação nas Fábricas. O Subsistema de Defeito-Zero engloba estas questões.
3. S3A – Subsistema de Pré-Requisitos Básicos / Troca Rápida de Ferramentas (SMED): Shingo inventou o chamado sistema SMED (Single Minute Exchange of Die and Tools) o que significa que o tempo de preparação de máquinas deve ser completado em no máximo nove minutos e 59 segundos. Shingo (1985) diz que o JIT constitui-se em um Princípio muito efetivo para a gestão dos Sistemas Produtivos, porém o JIT constitui-se em um fim e não um meio. Shingo (1985) postula que sem a compreensão das técnicas e métodos práticos que formam o coração do sistema o JIT não tem nenhum significado. E complementa “eu acredito firmemente que o sistema SMED é o método mais efetivo para implementar a produção Just-In-Time” (Shingo, 1985, p. xvii). Na verdade a Troca Rápida de Ferramentas é um elemento central dentro do contexto dos Sistemas de Produção com Estoque-Zero.
4. S3B – Subsistema de Pré-Requisitos Básicos/Operação-Padrão: O conceito de Operação-Padrão foi desenvolvido originalmente por Taiichi Ohno em uma Empresa Têxtil, que originou a Toyota, durante os anos 30 (Ohno, 1997). Conforme Ohno “a folha de trabalho padrão combina efetivamente materiais, trabalhadores e máquinas para produzir eficientemente” (Ohno, 1997, p. 22). De acordo com Ohno (1997) a Operação-Padrão exerce um importante papel na Toyota no que tange ao controle visual do trabalho na Fábrica. Em outras palavras, a Operação-Padrão objetiva balancear a carga de trabalho na manufatura, estabelecer uma seqüência de trabalho padrão e controlar o inventário visando manter a menor quantidade do mesmo para executar uma determinada seqüência de trabalho (Edwards et alli, 1993, p.08). De forma geral, dentro do STP a Operação-Padrão é utilizada em conjunto com a lógica das chamadas células de produção.
5. S3C – Subsistema de Pré-Requisitos Básicos/ Layout celular e produção em fluxo unitário: o princípio geral, do ponto-de-vista do STP, pode ser explicitado da seguinte forma: “a abordagem básica de um problema de Layout consiste em reduzir o transporte a zero” (Shingo, 1996b, p.273). Uma concepção mais geral implica na necessidade da adoção de Layouts que permitam simultaneamente, sempre que possível, alcançar a linearização do fluxo produtivo e responder com flexibilidade à(s) alteração(ões) do mix de produtos e do volume de produção.
6. S4 – Subsistema de Sincronização e Melhorias Contínuas: a partir das visitas de Taiichi Ohno a várias Empresas norte-americanas de automóveis, entre as quais a General Motors e a Ford, ficou impressionado com o funcionamento dos supermercados americanos (Ohno, 1997). Ohno diz que a razão para isso é que “no final da década de 40, na oficina da Toyota que eu gerenciava, já estávamos estudando os supermercados americanos e aplicando seus métodos ao nosso trabalho” (Ohno, 1997, p.45). Ohno estabeleceu uma relação entre a lógica de funcionamento dos supermercados e o sistema Just-In-Time. Conforme Ohno, “um supermercado é onde um cliente pode obter (1) o que é necessário, (2) no momento em que é necessário, (3) na quantidade necessária” (Ohno, 1997, p.45). Ohno observa que a partir do supermercado a equipe da Toyota passou a utilizar a lógica segundo a qual “o processo final (cliente) vai até o processo inicial (supermercado) para adquirir as peças necessárias (gêneros) no momento e na quantidade em que precisa” (Ohno, 1997, p. 45). Ohno e sua equipe percebiam os conceitos desenvolvidos nos supermercados americanos como essenciais para que a Toyota caminhasse no sentido da produção Just-In-Time. Em 1953, a Toyota iniciou a implantação do sistema baseado no supermercado via o método da “tentativa e erro” (Ohno, 1997, p. 45). Este sistema “mais tarde foi chamado de Sistema Kanban” (Ohno, 1997, p.47).
3.) A Relação entre os Diferentes Subsistemas do STP e as 7 Perdas nos Sistemas Produtivos – Uma Discussão Crítica
Uma análise da Tabela 1 possibilita tecer as seguintes observações críticas:
1. Os Subsistemas S3A – Troca Rápida de Ferramentas e S3C – Layout Celular constituem-se nos Subsistemas que atacam um maior número de Perdas nos Sistemas Produtivos. Portanto, sem sombra de dúvidas constituem-se em Pré-Requisitos básicos para a implantação do STP.
2. As Perdas por fabricação de produtos defeituosos dependem, para serem eliminadas, de praticamente todos os Subsistemas de Gestão envolvidos. Isto comprova a relação da melhoria da qualidade dos produtos (garantia da qualidade dos produtos) com os aspectos relacionados com temas vinculados à produtividade.
3. As Perdas por superprodução possuem um elevado grau de correlação com 4 Subsistemas (S1, S2, S3A e S4);
4. As Perdas ligadas a Função-Operação estão fortemente inter-relacionadas aos Subsistemas de Pré-Requisitos Básicos (S3A, S3B e S3C).
5. O Subsistema de Sincronização e Melhorias (S4) possui uma forte relação com a eliminação das Perdas por superprodução, estoque e por espera, mantendo um relacionamento moderado com as Perdas por transporte, por fabricação de produtos defeituosos e por movimento. Trata-se de um Subsistema importante para debelar as Perdas nos Sistemas Produtivos.
4.) A Inter-relação entre os Subsistemas do STP – Uma Discussão Crítica
A Tabela 2 abaixo mostra a inter-relação entre os Subsistemas dos Sistemas de Produção com Estoque-Zero.
Tabela 2 - Interação entre os diversos Subsistemas do Sistema Toyota de Produção
A partir do quadro acima pode-se depreender as seguintes observações de caráter qualitativo:
1. Existe um quadro de forte interação entre todos os Subsistemas. Pela Tabela 2 pode-se observar que existe uma forte interação em vinte das trinta interações possíveis entre os Subsistemas;
2. O Subsistema de Sincronização e Melhoria Contínuas apresenta a característica central de terem uma forte interdependência com todos os demais Subsistemas. Portanto, representa o subsistema central que garante o caráter dinâmico das melhorias contínuas dos Sistemas Produtivos.
3. O Subsistema de pré-requisitos básicos/operação padrão influencia todos os demais Subsistemas. Isto é corroborado pela proposição de Taiichi Ohno em seu livro ‘Sistema Toyota de Produção: Para Além da Produção em Larga Escala’, segundo a qual as ações embasadas na Operação-Padrão constituem-se em elementos centrais para a redução das variabilidades nos Sistemas Produtivos preparando-os para as futuras melhorias nos mesmos.
4. Para que seja possível estabelecer um bom Layout todos os Subsistemas devem estar funcionando de maneira correta. Isto explica porque, por exemplo, Black (1998) propõe em seu método que inicialmente seja feito um trabalho visando a melhoria radical do Layout, transformando-o em um Layout em fluxo contínuo.
5.) Conclusões
O Sistema Toyota de Produção constitui-se em fonte central para a competitividade da Empresas que querem tornar-se Fabricação Classe Universal. Porém, para que o Sistema possa ser compreendido em profundidade e utilizado em sua plenitude é necessário observá-lo, não a partir de suas técnicas isoladas, mas a partir de uma visão de inter-relacionamento sistêmico entre os diversos Subsistemas que o constituem e destes com a eliminação das Perdas nos Sistema Produtivos.
O presente artigo evidenciou os graus de inter-relacionamentos existentes entre os diversos Subsistemas que constituem o STP e as 7 Perdas nos Sistemas Produtivos. A partir da análise feita é possível observar explicitamente a relação entre os diferentes Subsistemas do STP e os seus objetivos no que tange a eliminação das Perdas nos Sistemas Produtivos.
Finalmente, o artigo mostra os inter-relacionamentos entre os diferentes Subsistemas que constituem o STP. Pode-se depreender da análise feita que, para que o STP possa funcionar da forma mais eficaz possível, é preciso compreender não só o conteúdo técnico de cada um dos Subsistemas como também os seus efetivos graus de interação e interdependência.
6.) Referências Bibliográficas
BLACK, J.T. O Projeto da Fábrica com Futuro. Editora Bookman, Porto Alegre, 1998.
GHINATO, Paulo. Sistema Toyota de Produção: mais do que simplesmente just-in-time. Caxias do Sul: Universidade de Caxias do Sul, 1996
LOCKAMY, A. & COX, J. F. Reengineering Performance Measurement: How to Align Systems, Products, and Profits. Irwin Professional Publishing, 1994.
OHNO, T. Sistema Toyota de Produção – Além da Produção em Larga Escala, Porto Alegre, Editora Bookman, 1997.
SHINGO, S. Sistema Toyota de Produção - do ponto-de-vista da Engenharia de Produção. Porto Alegre, Editora Bookman, 1996a.
SHINGO, S. Sistema de Produção com Estoque-Zero: O Sistema Shingo para Melhorias Contínuas. Porto Alegre, Editora Bookman, 1996b.