Auditoria da gestão do posto de trabalho no posto de trabalho
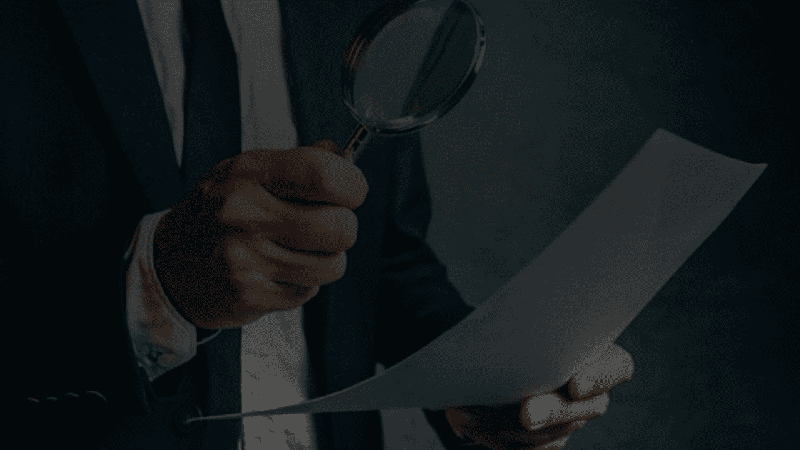
Por: Admin - 30 de Novembro de -0001
Em um texto anterior abordamos a metodologia de Gestão Lucrativa dos Postos de Trabalho – GPT, metodologia que possibilita o cálculo da eficiência operacional de um sistema de produção através do indicador de desempenho denominado Índice de Rendimento Operacional Global – IROG, que, como comentamos, deve ser analisado de acordo com duas abordagens conforme o posto de trabalho que está sendo analisado: i) o posto de trabalho é uma restrição do sistema de produção, sendo denominado Total Effective Equipment Produtivity – TEEP, utilizando-se, para seu cálculo, o tempo calendário; ii) o posto de trabalho é uma não restrição do sistema de produção, sendo denominado Overall Equipment Efficiency – OEE, utilizando-se para seu cálculo, o tempo programado, obtido pela diferença entre o tempo calendário e o tempo das paradas programadas.
Já elaboramos um texto sugerindo a realização de auditorias periódicas na organização, visando avaliar a consolidação dos conceitos do IROG como um todo, visto que a cultura dos conceitos do Sistema Toyota de Produção – STP, entre os quais se incluem os conceitos da GPT, deve estar disseminada amplamente entre todos os colaboradores. Neste texto iremos abordar a realização de auditorias periódicas em um determinado posto de trabalho, visando analisar quão implementada a metodologia GPT está nele implementada. Para tanto, utilizamos uma planilha adaptada de Nakajima, Seiichi, apresentada no livro TPM Development Total Productive Maintenance, Productivy Press, pg. 32, 1989, apresentada abaixo.
Conforme se observa, a planilha está formatada em função dos índices do IROG, quais sejam, Índice de Disponibilidade (µ1); Índice de Desempenho (µ2) e Índice de Qualidade (µ3), índices estes relacionados com tipos de perdas específicas de cada um.
Cada tipo de perda contém um conjunto de questões, pontuadas de 1 a 4, com o objetivo de verificar, no momento da auditoria, qual é a situação do posto de trabalho monitorado em relação a implantação da metodologia GPT, conforme os exemplos apresentados na sequência.
Vida útil do equipamento, relacionada a perda por quebra, vinculada ao µ1, com a seguinte pontuação: (1) vida útil do equipamento não é conhecida; (2) vida útil das peças do equipamento é estimada; (3) vida útil dos equipamentos é prolongada e (4) vida útil das peças do equipamento é previsível.
Setup, relacionada a perda por setup e ajustes, vinculada ao µ1, com a seguinte pontuação: (1) sem controle com setup realizado pelos operadores sem conhecimento dos conceitos de SMED (Troca Rápida de Ferramentas); (2) atividades de setup organizadas; (3) transferindo atividades internas de setup para atividades de setup externo e (4) tempo de setup menor do que 10 minutos.
Velocidade, relacionada a perda por queda de velocidade, vinculada ao µ2, com a seguinte pontuação: (1) não existe velocidade padrão (por produto ou por equipamento); (2) padrões de velocidade provisórios definidos e mantido por produto; (3) velocidade definida por produto. Relação de causa e efeito prevista entre o problema e a precisão do equipamento, dispositivo e ferramentas e (4) padrões de velocidade definitivos e definidos e mantidos por produto.
Pequenas paradas, relacionada a perda por queda de velocidade, vinculada ao ao µ2, com a seguinte pontuação: (1) perdas por pequenas paradas não conhecidas; (2) perdas por pequenas paradas analisadas quantitativamente (frequência e localização da ocorrência e produção perdida); (3) todas as causas de pequenas paradas analisadas, todas as soluções implementadas, condições favoráveis; (4) não existem pequenas paradas (possível existência de operações não identificadas).
Qualidade, relacionada a perda por falta de qualidade e retrabalho, vinculada ao µ3, com a seguinte pontuação: (1) problemas crônicos de qualidade são negligenciados; (2) problemas crônicos de qualidade estão quantificados (detalhes do defeito, frequência e produção perdida); (3) todas as causas de problemas crônicos de qualidade analisadas, todas as melhorias implementadas, condições favoráveis e (4) perda por qualidade entre 0,1% e 0%.
O somatório das pontuações é comparado com a pontuação máxima de 48 pontos, obtendo-se o percentual de implantação do indicador de desempenho IROG no posto de trabalho monitorado.
A partir da elaboração de um gráfico radar, em cujos raios é mostrada a pontuação média de cada um dos cinco tipos de perdas constantes na planilha, define-se o percentual de implantação dos conceitos do IROG, com base na situação atual do posto de trabalho monitorado, a saber: i) IROG não implantado; ii) IROG implantado; iii) IROG implantado, podendo melhorar e iv) IROG implantado a nível de excelência.
Analisando-se este gráfico, pode-se, na sequência, definir metas a atingir em um determinado período para cada um dos tipos de perdas. Sugere-se que as auditorias periódicas no posto de trabalho sejam realizadas a cada três meses no primeiro ano e, nos anos seguintes, semestralmente.