O Sistema Toyota de Produção e a Engenharia de Produção Lucrativa (Moreku): Construindo processualmente a competitividade nas empresas brasileiras
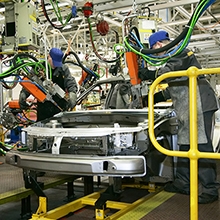
Por: Admin - 05 de Março de 2015
Os autores seminais que conceberam e implantaram o Sistema Toyota de Produção são Taiichi Ohno e Shingeo Shingo. Sendo assim, entender em profundidade os seus pensamentos e colocá-los em prática nas empresas é uma tarefa central de profissionais e pesquisadores que tratam do assunto. Vamos explorar, neste breve artigo, o tema central da Engenharia de Produção Lucrativa (Moreku) à la Toyota japonesa, que é pouco explorada na visão do Lean Manufacturing norte-americano.
Taiichi Ohno, em seu livro “O Sistema Toyota de Produção – Além da Produção em Larga Escala” (1997), utilizando uma abordagem socrática, faz a seguinte pergunta a seus leitores: “Qual a diferença entre a Engenharia de Produção tradicional (taylorista/fordista) e o Sistema Toyota?”. A resposta, fornecida pelo próprio autor, é de que a Toyota adota a noção de Engenharia de Produção Lucrativa (Moreku) dado que “... a não ser que a Engenharia de Produção resulte em redução de custos e aumento de lucros, eu acho que ela não tem sentido nenhum”.
O conceito proposto é fundamental para o projeto de sistemas produtivos sustentáveis do prisma da competitividade, por várias razões que serão brevemente expostas na sequência.
Em primeiro lugar, a necessidade de compreender que o objetivo/meta do Sistema Toyota de Produção, em sua forma original, está totalmente voltado a alcançar resultados econômico-financeiros eficazes (o que, posteriormente, será enfatizado e explicitado no pensamento teórico/prático proposto por Goldratt na Teoria Das Restrições – TOC). Em segundo lugar, que a montagem técnico-gerencial dos sistemas de produção deve levar em conta, para todos os casos – com total prioridade e foco – o tema da “microeconomia da firma”. Isto implica em compreender que não existem soluções de projeto de sistemas de produção únicos e universais, na medida em que os custos relativos dos fatores de produção (matéria-prima, trabalho e capital) são substancialmente distintos nos diferentes mercados (existem tanto diferenças regionais, que tendem a ser menores, como entre países, que são muito mais significativas). Em terceiro lugar implica na necessidade de desenvolver uma cultura de custos e ganhos em todos os funcionários da organização. A abordagem de Michikazu Tanaka, Gestor da Planta da Toyota de Daihatsu é explicita neste sentido: “O que você pensa que é a essência do Just-In-Time? A resposta do iniciante é que o JIT é bom simplesmente porque reduz o inventário. Uma resposta de nível intermediário é que o JIT permite a descoberta dos problemas e promove a sua solução através do kaizen. A terceira resposta, a mais madura, é que o JIT infunde uma consciência de custos em todos os empregados da empresa”.
O ponto, aqui, é ressaltar que Taiichi Ohno (e o Sistema Toyota de Produção em sua versão seminal de concepção e implantação) necessita ser ´lido´ e ´relido´ a partir da ótica de Engenharia de Produção Lucrativa (Moreku). Tomemos duas questões para exemplificar os argumentos aqui expostos:
a) teria sentido uma aplicação do Sistema Toyota de Produção nas empresas brasileiras hoje a partir da noção central da chamada Força Minimizada de Trabalho (FMT), ou seja, tendo foco principal a minimização das pessoas para a implantação do STP?
b) Por que no livro “O Sistema Toyota de Produção – Além da Produção em Larga Escala” (1997) não existem referências à utilização do chamado OEE – Overall Efficiecy Equipment (Índice de Rendimento Operacional Global – IROG) medidor central da abordagem do TPM?
Só é possível compreender e responder, na necessária profundidade, as questões expostas acima, se olharmos os aspectos objetivos relativos à “microeconomia da firma”. Neste caso, especificamente para os custos relativos dos fatores de produção trabalho e capital, no período e contexto específico de implantação do STP no Japão. Ocorre que, na época, como postula Shingeo Shingo em seu livro “Sistema Toyota de Produção – Do Ponto-De-Vista da Engenharia de Produção” (1996), o custo-hora das pessoas era aproximadamente cinco vezes maior do que a depreciação horária dos equipamentos. Ora, diante deste cenário econômico, o fator restritivo principal a ser considerado, para o projeto de melhoria no sistema produtivo, está associado ao trabalho (custo das pessoas) e não ao das máquinas (custo-horário relativamente mais baixo). Sendo assim, nada mais lógico de que o projeto do sistema produtivo da Toyota à época pudesse considerar eventualmente, inclusive, investimentos adicionais de máquinas, mas não das pessoas (fator de produção restritivo e proporcionalmente muito mais “caro”).
Isto teria sentido no Brasil de hoje, por exemplo, nas empresas que atuam no setor metal-mecânico? Por evidente, se comparado com o Japão (ou países como os EUA e a Alemanha). Como os custos relativos das máquinas é alto no Brasil, em relação às pessoas (variando entre a relação máquinas/pessoas de 1:1 ou 1:2), é essencial que tenhamos os nossos ativos atuando com elevada eficiência (particularmente nos gargalos produtivos).
Sendo assim, se Ohno estivesse vivo, hoje, no Brasil, certamente não iria abandonar a noção da Força Minimizada de Trabalho (uma vez que a racionalização da utilização da Força de Trabalho é relevante em todos os casos), mas daria atenção especial para o tema da máxima utilização dos ativos fixos (através da implantação, controle e melhorias do OEE), em particular as máquinas existentes nas empresas (levando em consideração o elevado custo relativo dos mesmos em muitas empresas brasileiras). Ou seja, o STP necessita ser percebido de maneira dinâmica, dado que as ações necessárias, da ótica da Engenharia de Produção Lucrativa, envolvem a noção de “alvo móvel” (tendo em conta a dinâmica de alteração dos custos relativos dos fatores de produção ao longo do tempo e do espaço) e não é admissível pensar na velha ideia taylorista do “the one and the best way” em termos dos enfoques de melhorias a serem adotadas.
No riquíssimo livro, intitulado “Gestão dos Postos de Trabalho” (2015), comemorativo aos 100 anos do nascimento de Taiichi Ohno, existe uma verdadeira preciosidade histórica escrita por ele no seu capítulo 20, cujo título chama-se “Aprendemos a fazer setup na forjaria da Toyota do Brasil”, que trata – com precisão – o conceito da Engenharia de Produção Lucrativa.
Na época da observação feita por Ohno, a Toyota do Brasil fabricava um volume muito baixo de quarenta carros/mês. Neste contexto, na forjaria existia apenas uma máquina que necessitava fazer mais de sessenta tipos de peças diferentes por mês.
Naquele tempo histórico, segundo Ohno, “essa deve ter sido a menor empresa automobilística do mundo” e, devido ao pequeno volume de compras envolvido, nenhum fornecedor se interessava em fornecer forjados para a Toyota. Em um trabalho excelente e árduo – desenvolvido em conjunto por profissionais brasileiros e japoneses – resultou, além da redução radical dos tempos de preparação (setup), no fato de que a empresa tornou-se capaz de fabricar “mais de sessenta variedades de peças sem provocar a perda de uma única peça”. A fábrica brasileira tornou-se tão eficaz que como resultado “os papéis se inverteram e mandamos duas ou três pessoas do Japão para aprender sobre setup de forjamento”.
Do prisma mais amplo, Ohno diz que “... à Toyota do Brasil estava efetivando o Sistema Toyota melhor do que qualquer outra unidade” e, apesar do baixo volume (em contraposição a produção em massa), a Toyota do Brasil estava tendo excelente desempenho econômico-financeiro, em uma situação que “... normalmente se esperaria que perdessem muito dinheiro”. As melhorias efetuadas no sistema produtivo da Toyota do Brasil – no sentido de flexibilizar a produção para o atendimento de uma demanda que acoplava variedade com baixo volume – à época, seguiram com rigor a máxima do Ohno, segundo qual a necessidade é a mãe da invenção’.
Mas, o mais importante do prisma da Engenharia de Produção Lucrativa aparece nas constatações finais do capítulo. O Sistema Toyota foi, inicialmente, construído para uma realidade da produção de baixos volumes e muita variedade (muitos modelos).
Neste sentido, ações como as relatadas por Ohno em relação ao desenvolvimento de tecnologias de processo e de gestão visando a redução dos tempos de preparação na Forjaria (e em outras partes da fábrica que produz em ´lotes´: fundição, usinagem, estamparia etc.) eram essenciais. Porém, na medida em que os volumes produzidos foram aumentando e as variedades tornando-se ainda maiores nas fábricas, a Toyota passou a produzir internamente utilizando o conceito central de takt-time na linha de montagem. De outra parte, os componentes/peças passaram a ser, cada vez mais, adquiridos de fornecedores (daí a importância do desenvolvimento de fornecedores e da adoção do Kanban entre a Toyota e seus fornecedores – e não mais somente o Kanban interno na própria Toyota). Sendo assim, as condições contextuais e ambientais se transformando, levaram a mudanças no âmbito do projeto e implantação do Sistema Toyota de Produção. Nas palavras de Taiichi Ohno, “na época em que começamos com o Sistema Toyota de Produção, tínhamos uma demanda de três a cinco mil veículos/mês e muita variedade.
O Sistema Toyota de Produção é um sistema que funciona muito bem quando aplicado às empresas de médio porte. O que quero dizer com isto é que o Sistema Toyota de Produção nasceu na época de volumes com dois a três mil veículos/mês e, hoje em dia, quando os volumes de produção na Toyota estão tão altos, não há necessidade de usar este sistema para reduzir custos. Ou seja, o Sistema Toyota continua tendo como foco a Engenharia de Produção Lucrativa, para diferentes contextos onde os volumes/demandas de mercado e a variedade se alteraram consideravelmente. No entanto, a concepção do STP, seus métodos e técnicas (Kanban, Troca Rápida de Ferramentas, etc.) precisam responder as necessidades dinâmicas do mercado e serem sempre utilizadas no sentido de aumentar os lucros e reduzir os custos das empresas. Isto exige diferentes projetos de sistemas de produção para distintas realidades.
A PRODUTTARE adota diretamente o conceito de Engenharia de Produção Moreku. Isto implica em evitar, sistematicamente, a adoção de soluções prontas e universais, e a ideia de que existem métodos e técnicas milagrosas que resolvem todos os problemas para todas as empresas, em qualquer momento do tempo. A ideia perseguida consiste em tratar as diferentes situações e contextos econômicos de forma dinâmica e específica, tendo como pontos centrais: I) uma compreensão ampla da microeconomia da fábrica e seus desdobramentos em termos dos custos dos fatores de produção envolvidos (capital, trabalho, energia, matérias-primas e materiais); II) possuir um modelo/framework de referência, que intitulamos de Sistema PRODUTTARE de Produção, e que deve ser dinamicamente adaptado e melhorado levando em conta o contexto microeconômico e a estratégia de negócios e produção de cada empresa em particular. Tal tema será abordado em nossos próximos artigos.
Junico Antunes
Diretor da Produttare Consultores Associados