Os índices de Eficiência Operacional dos Equipamentos
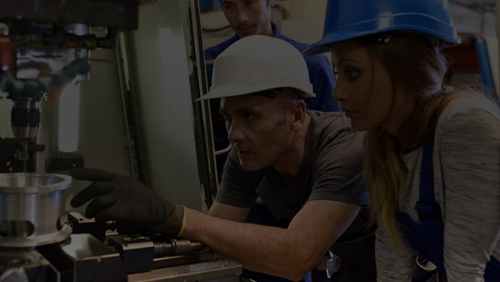
Por: Admin - 15 de Junho de 2022
NÃO DEIXE O SEU PROCESSO DE PRODUÇÃO LHE DOMINAR. DOMINE-O VOCÊ!
"Mas como?", você perguntará. A resposta para esta pergunta é muito simples: implante a metodologia da Gestão Lucrativa dos Postos de Trabalho – GPT, a partir da qual se pode calcular o índice de rendimento operacional dos postos de trabalho de seu processo de produção, denominado Índice de Rendimento Operacional Global – IROG (já apresentado anteriormente), que tem duas abordagens conforme o posto de trabalho seja uma restrição (então denominado Effective Equipment Produtivity – TEEP), ou não (então denominado Overall Equipment Efficiency – OEE), sigla amplamente conhecida.
O valor do IROG em um posto de trabalho é calculado pela divisão do tempo de agregação de valor em relação ao tempo disponível para produzir. Por exemplo, em um turno de 08 horas, caso o tempo real de produção, ou seja, de agregação de valor, for de 4,0 horas, o valor do IROG será de 50,0%.
Este valor, por si só, indica que há um considerável potencial de melhorias a ser feito no posto de trabalho monitorado, uma vez que apenas a metade do tempo em que ele está disponível para produzir, ele agrega valor. Esta conclusão já indica que você pode começar a dominar o seu processo de produção a partir da implantação de ações de melhoria em seu posto de trabalho gargalo, visando aumentar a sua produtividade e reduzir os custos de produção.
Mas... como saber onde realizar estas ações de melhorias, uma vez que se deve atuar sobre as causas básicas das ineficiências detectadas, no sentido de evitar a sua recorrência?
Para identificarmos as causas básicas das ineficiências, faz-se necessário desmembrar o IROG em seus índices, considerando a fórmula:
IROG = µ1 x µ 2 x µ 3, onde:
- µ1 = Índice de Disponibilidade, relacionado às paradas do posto de trabalho;
- µ2 = Índice de Desempenho, relacionado a queda de velocidade e pequenas paradas;
- µ3 = Índice de Qualidade, relacionado à não conformidade dos produtos.
O registro das paradas, tanto programadas, como por exemplo manutenção preventiva, como paradas não programadas, como por exemplo quebra do equipamento, deve ser feito em um diário de bordo ou coletor eletrônico de dados, permitindo posteriormente o cálculo do Índice de Disponibilidade através de sua fórmula específica:
µ1 = (Tempo disponível – tempo de paradas) / Tempo disponível
Exemplificando, no caso citado, tendo-se registrado 3,5 horas de paradas, devidamente identificadas através de uma tipologia, obtém-se:
µ1 = (8,0 horas – 3,5 horas) / 8,0 horas = 0,562 ou 56,2%
Da mesma forma, deve-se registrar a quantidade de itens conformes e não conformes, permitindo posteriormente o cálculo do Índice de Qualidade, através de sua fórmula específica:
Supondo-se que no exemplo, durante o tempo disponível foram produzidas 390 unidades conformes de um produto cujo tempo de ciclo é de um minuto e 10 unidades não conformes, obtém-se:
µ3 = 390 / (390+10) = 0,975 ou 97,5%
Já o Índice de Desempenho, de difícil registro, pode ser calculado a partir da fórmula do IROG apresentada anteriormente:
µ2 = IROG / µ1 x µ3
Aplicando-se nesta fórmula os valores já calculados, obtém-se:
µ2 = 0,500 / 0,562 x 0,975 = 0,911 ou 91,1%
É importante destacar que a utilização desta fórmula possibilita identificar, também, distorções nos dados, como registros incorretos do tempo de paradas no diário de bordo ou tempo de ciclo dos produtos incorretos registrados no sistema, resultando em valores extremamente baixos ou altos.
Em empresas de classe mundial, como referência, pode-se considerar os valores de 85,0% para o IROG; 90,0% para o Índice de Disponibilidade; 95,0% para o Índice de Qualidade e 90,0% para o Índice de Desempenho, segundo Nakajima, o autor que propôs estes índices no livro Total Productive Maintenance.