Total Productive Management (TPM) – O Pilar de Melhoria Focalizada
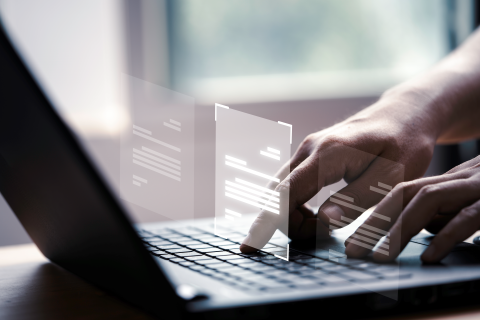
Por: Admin - 30 de Novembro de -0001
Neste vídeo, João Cunha, consultor da Produttare, engenheiro mecânico, mestre em engenharia da produção, com experiência de mais de 25 anos em Total Productive Management (TPM), apresenta as perdas e desperdícios que podem ser identificadas no processo de implantação do TPM.
Quando falamos sobre TPM, muitos relacionam à área de manutenção da empresa, visto que a tradução do termo carrega a palavra Manutenção.
Contudo, TPM, ou seja, Gestão Produtiva Total, diz respeito a manter e conservar os equipamentos e produtividade através da gestão da produtividade como um todo.
Este vídeo foi extraído do evento online "Como a RHI Magnesita alavancou a eficiência em 20% nos postos de trabalho críticos". Clique aqui para assistir o webinar na íntegra.
Total Productive Management (TPM)
A TPM é uma metodologia composta por 8 pilares:
- Melhoria Focalizada;
- Manutenção Autônoma;
- Manutenção Planejada;
- Manutenção da Qualidade;
- Gestão Antecipada;
- TPM nas Áreas Administrativas;
- Educação e Treinamento;
- Saúde, Segurança e Meio Ambiente.
O vídeo detalha o primeiro pilar, Melhoria Focalizada, apresentando as perdas e desperdícios que podem ser encontrados na implantação deste pilar.
Visto que TPM é base da metodologia World Class Manufacturing (WCM), este pilar também está presente como Melhoria Focada e Cost Deployment no WCM.
Buscando um menor custo operacional e geração de valor ao cliente, são utilizados os conceitos e métodos previstos em Engenharia Industrial (EI), Total Quality Management (TQM), Total Productive Management (TPM) e Just in Time (JIT).
Através da implantação do WCM ou TPM, as empresas buscam zero estoque aplicando o just in time.
Já para alcançar zero defeitos, pode ser utilizado a Gestão da Qualidade Total (TQM).
Para o ataque aos desperdícios são utilizadas as técnicas e ferramentas da Engenharia Industrial.
Por fim, a TPM constrói uma mudança de cultura na empresa que visa zero perdas nos postos de trabalho.
A TPM, o WCM, o TQM e o JIT estão fortemente conectados na busca da redução de perdas e desperdícios do fluxo de transformação.
Fluxo da melhoria focalizada
Antes de buscar a melhoria focalizada, é preciso que as dimensões estratégicas do negócio estejam bem definidas. Sugere-se que sejam baseadas no PQCD:
- P: Capacidade produtiva e produtividade;
- Q: Qualidade;
- C: Custo;
- D: Atendimento ao cliente.
Para que as dimensões estratégicas do negócio sejam atendidas, é necessário que sejam entendidos adequadamente os fatores externos e internos que influenciam no resultado do negócio, identificando as necessidades de melhorias em PQCD, a fim de tornar a empresa competitiva.
Com isso, é possível definir os fatores críticos e as prioridades a serem atacadas em PQCD e identificar os pontos chaves, ou seja, metodologias e ferramentas, necessários para eliminar as perdas e os desperdícios.
Após a identificação dos fatores críticos e pontos chaves, é necessário executar o desdobramento das perdas e desperdícios em PQCD até o nível operacional, a fim de construir o plano de ação para mensurar futuramente os resultados das melhorias.
Todo este fluxo de definições e identificação dos fatores que influenciam o sistema produtivo, auxiliam a equipe a concentrar as energias na produção para atacar as perdas e os desperdícios, entregando resultados à alta direção.
Teoria das restrições
Antes de falarmos sobre perdas e desperdícios do pilar da Melhoria Focalizada, é necessário que tenhamos o entendimento sobre a Teoria das Restrições.
Esta metodologia nos permite identificar a restrição, ou seja, o gargalo do sistema, visto que é ele o definidor do fluxo. Sabe-se que, a produção do gargalo, será a produção do sistema.
O grande desafio das organizações é escolher o posto de trabalho crítico para monitoramento e melhoria da sua eficiência e consequente liberação de capacidade nesse fluxo produtivo.
Para auxiliar nesta escolha e localizar as restrições do processo produtivo, sugere-se que seja utilizado um mapeamento do fluxo de valor, por exemplo, o mapeamento do Shingo.
Protegendo o gargalo com um pulmão e sincronizando através da metodologia de corda, é possível manter o gargalo bem abastecido e o mercado atendido, assim como elevando a eficiência de todo o fluxo a partir do aumento da eficiência do gargalo.
Para o aumento da eficiência do sistema produtivo é importante atentar-se a outras perdas e não somente às perdas com os equipamentos, como as que ocorrem no processo, relacionadas à mão de obra, energia, materiais etc.
Perdas e desperdícios no processo
Segundo Shingo, são 7 as perdas que podem ser encontradas no processo:
- Superprodução: esta perda acontece quando a produção fabrica produtos em excesso, acima da demanda do mercado;
- Transporte: quando o produto é transportado de maneira inadequada, percorrendo por caminhos desnecessários;
- Processamento desnecessário: esta perda ocorre quando há excesso de etapas no processamento dos produtos, ou seja, etapas desnecessárias;
- Movimentação: refere-se às movimentações desnecessárias dos colaboradores durante o processo;
- Espera: acontece quando o produto fica aguardando processamento entre etapas;
- Defeitos: perda que ocorre por falta de qualidade, quando um produto está fora dos padrões pré-estabelecidos;
- Estoques: refere-se ao excesso de estoque de materiais e produtos, que geram gastos desnecessários e ocupa espaço físico.
Perdas e desperdícios no posto de trabalho
Também há as perdas e os desperdícios ligadas ao posto de trabalho, como as relacionadas à mão de obra, à energia, materiais, moldes e equipamentos.
Perdas relacionadas à mão de obra
Podemos encontrar cinco perdas relacionadas à mão de obra:
- Perda por esperas: tempo de espera por materiais, ferramentais, instruções, reparos etc;
- Perdas por deficiência administrativa: perdas por baixo desempenho dos equipamentos, deficiência de métodos e por falta de conhecimento;
- Perdas por desorganização: perdas por procura de objetos e procura por informações;
- Perdas por movimentação: tempo de mão de obra gasto em trabalhos logísticos (transporte de produtos, deslocamento de matérias primas etc.) executados por colaboradores cujas atribuições não incluem tais funções;
- Perdas por medições e ajustes: tempo gasto em medições e ajustes demasiadamente frequentes, executados como medidas preventivas contra recorrência ou descarte de materiais e/ou produtos defeituosos.
Perdas relacionadas à energia
É constituída pela energia investida (eletricidade, gás, combustíveis etc), que não é utilizada com eficiência no processamento industrial.
Também inclui as perdas decorrentes de acionamento, as perdas de temperatura durante o processamento e as perdas por tempo ocioso (funcionamento sem carga).
Perdas relacionadas a materiais
Corresponde a diferença entre a quantidade das matérias-primas utilizadas na fabricação e a quantidade dos respectivos produtos acabados com qualidade aprovada.
Nesta categoria estão incluídas as perdas correspondentes a materiais defeituosos, perdas de fio de corte e perdas de peso.
Perdas relacionadas a moldes, ferramentas e gabaritos
São constituídas pelas despesas adicionais efetuadas para substituição ou recondicionamento de moldes, ferramentas e gabaritos, decorrentes tanto de quebras quanto de desgastes pelo uso.
Este tipo de perda inclui os respectivos materiais de apoio, tais como óleo de corte, óleo de fresagem/usinagem etc.
Perdas relacionadas a equipamentos
Para identificar estas perdas, deve ser analisado se a máquina está para ou trabalhando e se está trabalhando com sua performance prevista. Também analisa o tempo desperdiçado nas máquinas na produção de produtos defeituosos.
São oito as perdas relacionadas à disponibilidade, performance e qualidade dos equipamentos:
- Perda por falta de programação: tempo de máquina ocioso por falta de carga ou parada programada;
- Perdas por quebras em equipamentos: são paralisações na função que ocorrem inesperadamente, cuja duração é acima de 15 minutos;
- Perdas por setup e ajustes: período de inatividade quando equipamentos são preparados para a produção;
- Perdas por trocas de lâminas de corte: paralisação da linha para reposição de esmeris, fresas, brocas etc, devido à quebras ou por estarem sem afiação;
- Outras perdas com parada: limpeza, espera (instruções, materiais, distribuição de pessoal e verificação de qualidade etc);
- Perda por pequenas paradas e operações em vazio: parada ou inatividade dos equipamentos durante pouco tempo, devido a problemas temporário e de curta duração (menor que 15 minutos);
- Perda por velocidade: diferença entre a velocidade projetada para operação do equipamento e a velocidade real de seu funcionamento;
- Perda por defeitos: produtos defeituosos gerados durante a fabricação ou no início de produção de um novo produto.
Conclusão
TPM é uma metodologia voltada à manutenção da produtividade, ou seja, focada em elevar a produtividade da empresa por meio de oito pilares.
Um dos pilares mais importantes é a Melhoria Focalizada, responsável por elevar a disponibilidade, performance e qualidade do processo e postos de trabalho.
Com a definição das estratégias da empresa e a análise das restrições do processo, é possível implantar a melhoria focalizada e melhorar a eficiência da produção, agregando valor ao cliente.
Assim, a partir do entendimento das perdas de processo e dos postos de trabalhos, é possível identificá-las e eliminá-las, focalizando esforços e melhorando a produtividade.