Uma abordagem metodológica para o gerenciamento das restrições dos sistemas produtivos: A gestão sistêmica, unificada/integrada e voltada aos resultados do Posto de Trabalho
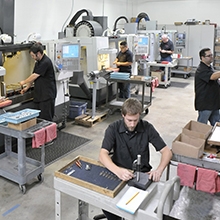
Por: Admin - 12 de Dezembro de 2014
Autores
José Antonio Valle Antunes Júnior
Universidade do Vale do Rio dos Sinos – UNISINOS e PRODUTTARE Consultores Associados
Marcelo Klippel
Pontifícia Universidade Católica do Rio Grande do Sul - PUCRS e KLIPPEL Consultores Associados
Abstract
This paper describes the concept of Workplace Management, based on principles, concepts and techniques of Theory of Constraints – TOC and Toyota Production System – TPS. It proposes the use of a methodology entitled “Workplace Management: A Systemic Approach, Unified/Integrated and Focused on The Bottom Line Results”, that allows an organization to reach satisfactory economical results, with the focus in the management of the main constraints of the system.
Key Words: Workplace, Management, Productivity
1. A Problemática de Trabalho
Uma das questões relevantes em termos da Gerência da Produção nas Organizações se refere à Gestão do Posto de Trabalho (GPT). Discussões sobre a problemática das Rotinas e das Melhorias nos Postos de Trabalho acompanham a história da Engenharia de Produção. Os trabalhos originais de Taylor e Gilbreith e de seus seguidores, trataram do tema desde o início do século XX. Porém, no mundo moderno o conceito de Sistema e suas implicações vem alterando sobremaneira a forma de pensar sobre os Sistemas Produtivos. Os conceitos, princípios e técnicas do Sistema Toyota de Produção e da Teoria das Restrições propugnam a necessidade de modificar a forma como o GPT vem sendo realizado nas Organizações Modernas. Este trabalho procura evidenciar uma metodologia prática de tratar o problema tendo como base os modernos princípios e técnicas ligadas a Engenharia de Produção.
Em relação à problemática da Gestão dos Postos de Trabalho – GPT nas Empresas observa-se que várias ações são realizadas no cotidiano das Empresas, envolvendo diretamente os operadores e as máquinas, entre as quais pode-se citar: i) A gestão da produtividade (peças/hora) dos Postos de Trabalho, realizada basicamente pelos profissionais da produção; ii) A gestão da eficiência dos equipamentos, atividade que, em geral, possui um coordenador geral ligado a área do TPM – Manutenção Produtiva Total; iii) Profissionais relacionados com a implantação do 5S no Posto de Trabalho; iv) Melhorias em termos dos atuais tempos de preparação de máquinas; v) Os analistas de qualidade são responsáveis pela problemática da geração dos refugos/sucatas e retrabalhos em Postos de Trabalho; vi) Analistas de Processo que tratam da questão da melhoria dos tempos de processamento das máquinas; vii) Desenvolvimento de profissionais vinculados com a problemática da segurança do trabalho e da Ergonomia.
A Figura 1 abaixo ilustra o conjunto de questões que, simultaneamente, tende a preocupar os profissionais/operários que atuam junto às máquinas.
Figura 1 – Relações dos Trabalhadores no Posto de Trabalho e das Funções de Gestão da Empresa
Algumas questões centrais surgem ao observar globalmente a problemática da GPT. Entre estas pode-se citar:
• Quais são as prioridades que devem ser seguidas pelos operadores no que tange as Rotinas e Melhorias a serem realizadas no Posto de Trabalho?
• As prioridades de ações no dia a dia, em termos de todos os Postos de Trabalho, devem ser as mesmas? Se não, como definir estas prioridades para cada caso em particular?
• Todos os Postos de Trabalho devem ser gerenciados de forma similar?
• Existe algum indicador capaz de envolver e integrar os diferentes atores que trabalham junto ao Posto de Trabalho? Como este indicador pode auxiliar na lógica de gerenciamento da Rotina e das Melhorias no Posto de Trabalho da Empresa?
Importante perceber que as ações concretas de melhorias nas máquinas, em particular as críticas, pressupõe uma ação conjunta das pessoas responsáveis por: processo, manutenção, troca rápida de ferramentas, qualidade, produção, ergonomia... Neste sentido é preciso ‘romper’ as lógicas segmentadas de tratamento do problema da GPT nas Empresas.
Faz-se necessário conceber uma GPT que leve em consideração os seguintes tópicos gerais: i) Focalizar as ações de gestão das rotinas e melhorias nos pontos críticos do sistema, que são os gargalos, os recursos com capacidade restrita – os CCR’s – e os postos que geram refugos e retrabalhos, ou seja, apresentam problemas relacionados com a qualidade; ii) Utilizar um medidor de eficiência nestes Postos de Trabalho que permita e estimule a integração entre produção, qualidade, manutenção, processo, melhorias de troca de ferramentas e afins; iii) Realizar planos de melhorias sistêmicos, unificados e voltados aos resultados globais da Empresa; iv) Avaliar os Postos de Trabalho críticos levando em consideração os indicadores e os respectivos planos de ação de melhorias. A seguir são apresentadas, sucintamente, as bases conceituais da Metodologia proposta.
2. O Referencial Teórico
O Sistema Toyota de Produção, segundo seus autores clássicos Shigeo Shingo (1996a, 1996b) e Taiichi Ohno (1997), deve ser interpretado a partir de duas óticas gerais inter-relacionadas desde um ponto-de-vista sistêmico.
A primeira ótica relaciona-se com um foco principal: as melhorias dos processos da Empresa. Em outras palavras, trata-se da efetivação de melhorias incrementais e radicais do fluxo de matérias-primas e/ou materiais no tempo e no espaço. Pode-se ainda dizer que estas melhorias dos processos seguem duas vertentes inter-conectadas que são: i) Sincronização da Produção e; ii) Melhorias nas operações mais lentas do sistema produtivo (‘as tartarugas’ na metáfora utilizada por Taiichi Ohno (1997). A materialização desta ótica basicamente ligada a sincronização do processo, e da melhoria sistemática destes processos, é realizada no âmbito do Sistema Toyota de Produção através da utilização de duas ferramentas básicas: o Kanban e a idéia de Takt-Time - que está vinculado diretamente com a noção de fluxo unitário de peças. É importante deixar claro que existem outras formas de gestão do fluxo de materiais na Empresa entre as quais pode-se encontrar: i) Os sistemas clássicos do tipo MRP/MRP II – tanto em termos de software como manuais –; ii) A lógica do tipo Tambor-Pulmão-Corda (TPC) defendida no âmbito da Teoria das Restrições (Goldratt, 1997).
A segunda ótica relaciona-se com a necessidade de gerir da melhor forma possível os ‘Postos de Trabalho’. Trata-se aqui da gestão conjunta e unificada das pessoas e das máquinas (a partir de uma ótica mais ampla a GPT pode envolver muitas outras questões além das pessoas e dos equipamentos tais como: ferramental utilizado, instruções de trabalho, aspectos ligados à ergonomia, gestão dos recursos humanos, etc.). Como base para esta análise será adotada a visão da chamada Gestão Sistêmica, Unificada/Integrada e voltada para as melhorias do processo ou, alternativamente, voltada para os resultados. Sob o ‘chapéu’ da GPT, mais particularmente a partir da utilização do item de controle intitulado de IROG, podem ser analisados um amplo conjunto de tópicos entre os quais pode-se incluir: troca rápida de ferramentas, paradas das máquinas devido a problemas de manutenção propriamente dita, queda de velocidade das máquinas (processo), qualidade (refugos e retrabalhos), operação em vazio da máquina, falta de operadores, etc. Importante perceber que, na lógica do Sistema Toyota de Produção como pode e é evidenciado na prática nas fábricas que utilizam ampla e plenamente o Sistema Kanban, as melhorias no Posto de Trabalho devem ser executadas a partir das operações que restringem a correta operação do sistema de produção tanto em termos qualitativos como quantitativos.
A Teoria Das Restrições – TDR – propõe que os Sistemas de Produção sejam geridos a partir das restrições visando alcançar a meta de ‘Gerar Dinheiro Hoje e no Futuro’. Para isso propugna a adoção dos Indicadores Globais – Lucro Líquido, Retorno Sobre o Investimento e Caixa e Indicadores Operacionais que são: Ganho, Despesas Operacionais e Inventários. A TDR utiliza os 5 passos expostos abaixo (Antunes, 1998):
Passo 1 – Identificar as restrições do sistema;
Passo 2 – Utilizar da melhor maneira possível as restrições do sistema;
Passo 3 – Subordinar todos os demais recursos a decisão tomada no Passo 2;
Passo 4 – Elevar a Capacidade das Restrições;
Passo 5 – Voltar ao passo 1, não deixando que a inércia tome conta do sistema.
Do ponto-de-vista específico deste trabalho dois conceitos são importantes: o de Gargalo e o de Recursos com Capacidade Restrita (Capacity Constraints Resources - CCRs). O(s) recurso(s) gargalo(s) pode(m) ser definido(s) como aqueles onde a Capacidade de Produção é inferior a Demanda. Os Recursos com Capacidade Restrita são aqueles em que em média a Capacidade é Superior a Demanda, porém devido a um conjunto de aspectos conjunturais (ex. Programação incorreta de produção, falta de matérias-primas, mix de produtos, problemas associados a manutenção, tempos de setup etc...) acabam restringindo o desempenho global do sistema (Antunes, 1998). Ao contrário dos gargalos, no caso dos recursos CCRs os problemas estão associados a gestão dos recursos e não a aquisição dos mesmos.
3. O Modelo Proposto
A partir das considerações gerais realizadas acima apresentadas propõe-se um modelo geral da Gestão Sistêmica, Unificada/Integrada e Voltado para os Resultados. A Figura 2 apresenta a estrutura geral proposta para a GPT.
Figura 2 - Sistema de Gestão do Posto de Trabalho
Para apresentar a lógica interna do Modelo de Gestão Sistêmico proposto, utiliza-se a Figura 3, a qual compreende quatro elementos fundamentais: i) Entradas do Sistema; ii) Processamento propriamente dito; iii) Saídas do Sistema; iv) Treinamento e; v) Gestão do Sistema.
Figura 3 - Estrutura de Gestão do Posto de Trabalho
A seguir apresentam-se os cinco elementos fundamentais da estrutura da GPT.
1. Entrada do Sistema – Em linhas gerais a idéia deste sistema consiste em melhorar os fluxos produtivos. Neste sentido, o primeiro ponto importante de ser explorado consiste na definição do conjunto de Postos de Trabalho que serão considerados gargalos, recursos com capacidade restrita – os CCR’s e os recursos que são críticos por apresentarem problemas relacionados com a qualidade (refugos e retrabalhos).
Para isso devem ser utilizadas informações gerais que são: i) Informações relativas a Capacidade e a Demanda provenientes do Planejamento, Programação e Controle da Produção e dos Materiais - PPCPM (Esta situação evidencia a importância do engajamento do pessoal do PPCPM na equipe multidisciplinar que constitui a equipe de Gestão Sistêmica, Unificada/Integrada e Voltada aos Resultados da Organização); ii) Informações e ‘sentimentos’ da realidade global do sistema provenientes dos programadores da produção; iii) Informações oriundas dos supervisores da fábrica e dos profissionais que atuam no chão-de-fábrica; iv) Informações provenientes dos analistas de qualidade para a definição dos Postos de Trabalho com problemas de qualidade. As informações para definição das máquinas gargalos e CCR’s podem ser provenientes de um Sistema de PPCPM, preferencialmente um software de Programação Fina da Produção - PFP - que utiliza informações cadastradas no Banco de Dados da empresa.
Um segundo tipo de informação prática refere-se as anotações realizadas no Diário de Bordo - DB. Este DB deve estar fixado junto ao Posto de Trabalho e as informações devem ser preenchidas diretamente pelo operador (basicamente informações relativas as paradas, produção, qualidade). Um ponto importante é que, para o preenchimento correto do DB, é necessário uma definição prévia da tipologia de paradas a ser adotada pela Empresa. Estas informações devem ser alimentadas no dia-a-dia pelo profissional designado pela Empresa, sendo o mesmo disponibilizado na rede para que todos possam ter acesso a sua consulta.
As definições a partir do Sistema de Planejamento de Produção em conjunto com as informações repassadas pelo Analista da Qualidade alimentam o Sistema de Monitoramento das Restrições, que representa o elemento central e fundamental da Gestão Sistêmica, Unificada/Integrada e Voltada para os Resultados no Posto de Trabalho apresentada no próximo item.
2. Processamento – Uma vez definido os Postos de Trabalho críticos, é necessário estabelecer conceitualmente um método geral para a abordagem da gestão da Rotina e da Melhoria dos mesmos. Propõe-se a adoção de uma lógica de uma Gestão Sistêmica, Unificada/Integrada e Voltada para os Resultados. Na verdade, isto não sugere nenhum tipo de inovação gerencial radical, mas sim a reordenação e reconceituação das práticas já existentes. Isto em três sentidos básicos: i) Visão sistêmica da fábrica como um todo – o que implica na subordinação da utilização dos recursos de melhorias dos Postos de Trabalho em determinados locais da organização; ii) Integrada/Unificada – na medida em que as ações nestes Postos de Trabalho devem ser feitas de forma conjunta entre os profissionais envolvidos; iii) Voltada aos Resultados – ou seja, melhorias nos indicadores destes Postos de Trabalho específicos devem levar a melhoria dos resultados gerais da Empresa. Pragmaticamente falando, trata-se de implantar a GPT sob uma nova ótica.
Faz-se necessário o cálculo das eficiências dos Postos de Trabalho. Este cálculo de eficiências é realizado a partir do cálculo do IROG, proposto originalmente pelos profissionais que atuam na área da Manutenção Produtiva Total (Nakajima, 1988). As medidas devem ser diárias e sistemáticas. Conceitualmente, é preciso perceber que a adoção do IROG e principalmente a melhoria do mesmo, pressupõe uma ação integrada entre os profissionais responsáveis pela produção, manutenção em seu sentido estrito, qualidade, processo, grupos de melhorias de troca rápida de ferramentas, etc. O IROG pode ser calculado a partir da Equação 1 ou 2:
Ou seja, o IROG é calculado através da multiplicação do Índice do Tempo Operacional (ITO) pelo Índice de Performance Operacional (IPO) pelo Índice de Produtos Aprovados (IPA). O ITO consiste no tempo total em que a máquina ficou disponível, excluindo-se as paradas que ocorrerem por diversos motivos. O IPO representa os tempos de operações em vazio, paradas momentâneas e quedas de velocidade. Estas paradas são de difícil visualização. Por fim, o IPA representa o tempo total de produção de peças boas, excluindo o tempo gasto com sucata e retrabalho.
O IROG também pode ser calculado a partir da equação acima. Ou seja, é encontrado pela razão entre o somatório do tempo de uma determinada peça multiplicado pela sua quantidade, pelo tempo total disponível da máquina.
O IROG não deve ser calculado da mesma maneira para todos os Postos de Trabalho. Nos recursos críticos o IROG deve assumir o conceito de TEEP – Total Effective Equipment Productivity – Produtividade Efetiva Total do Equipamento. A idéia é que o tempo total disponível de um recurso crítico deve ser o tempo total sem excluir nenhum tipo de parada programada. Neste caso, trata-se de calcular a produtividade real do sistema no gargalo.
Para o cálculo do IROG das demais máquinas é utilizado o OEE – Overall Equipment Efficiency – Índice de Eficiência Global. Neste caso o tempo total disponível é calculado pela subtração do tempo total das paradas programadas. Os recursos não críticos não precisam e não devem funcionar em tempo integral, na medida em que só seriam gerados estoques intermediários. O OEE deve ser entendido como a maneira como o sistema funcionou quando o mesmo foi requisitado para trabalhar.
3 - Saídas do Sistema – O Sistema de Monitoramento das Restrições – SMR - tem como resultado aspectos direcionados com o gerenciamento das Rotinas e das Melhorias na Empresa. Estes resultados fornecem informações gerenciais relevantes para os pontos estratégicos da Organização. Quanto a Rotina, os gráficos de eficiências - IROG devem ser fixados junto ao Posto de Trabalho para acompanhamento constante do operador e da supervisão. Devem ser tomadas ações gerenciais sempre que a eficiência do Posto de Trabalho caia abaixo do padrão de eficiência mínimo estabelecido. Quanto às melhorias, a partir das percepções das causas de queda do IROG, são elaborados Planos Detalhados de Melhorias para os Postos de Trabalho críticos, segundo uma lógica do tipo 5W1H.
As informações gerenciais geradas pelo SMR são enviadas para pontos estratégicos da Organização. Estas informações são os Gráficos de Eficiência (Diário, Mensal e Anual), Plano de Melhorias (5W1H), Tratamento de Anomalias, entre outros. Os destinos destas informações são, geralmente: Gerência Industrial, as Unidades de Manufatura e o Coordenador de Melhorias. Este conjunto amplo de informações agrupados no SMR deve realimentar o Banco de Dados da Organização, o qual deve conter as informações mais atualizadas do sistema real.
4- Treinamento – Visando suportar o funcionamento da GPT é necessário realizar o treinamento/capacitação de todos os envolvidos no processo. Estes treinamentos devem compreender os envolvidos na operação do diário de bordo, no cálculo do IROG e na concepção geral da Gestão Sistêmica, Unificada/Integrada e Voltada para os Resultados no Posto de Trabalho. Estes treinamentos devem ser efetuados exaustivamente sempre que haja a necessidade de aprimorar e/ou capacitar as pessoas na metodologia proposta.
5- Gestão do Sistema – As informações geradas pelo sistema possibilitam a Gestão do Sistema como um todo. Do prisma do método de operacionalização prática deste Sistema de GPT, ou seja da Gestão, sugere-se a montagem de um conjunto de reuniões específicas que são: reuniões freqüentes entre os gerentes/supervisores de produção com a equipe de trabalho envolvida nos trabalhos, reuniões mensais com a Gerência Industrial para apresentação e discussão dos resultados alcançados durante o mês de trabalho e workshops de melhorias com todos os envolvidos nesta Gestão Sistêmica, Unificada/Integrada e Voltada para os Resultados no Posto de Trabalho. Estas reuniões são essenciais para que o Sistema de Gestão possa proporcionar as Empresas os Resultados desejados.
4. Resultados da Aplicação do Modelo Proposto na Prática
Os resultados passíveis de serem obtidos através da aplicação do Método Proposto são:
• No caso da existência de gargalos internos ao Sistema Produtivo poderá será alcançado uma melhoria do TEEP, com a utilização de um nível baixo de Investimento, o que acarretará ganhos significativos no desempenho econômico da Empresa;
• O controle do desempenho da Rotina dos Equipamentos permite obter o desempenho econômico global projetado pela Empresa, sem a utilização de recursos adicionais (exemplo: utilização de horas-extras, contratação de pessoal desnecessariamente etc...);
• Permitir a Gestão Global do Sistema Produtivo com foco nas restrições. Ou seja, os gerentes, supervisores e trabalhadores podem focar seus esforços de melhorias nos Postos de Trabalho críticos (gargalos, CCRs e recursos com problema de qualidade);
• O Sistema permite a definição da Capacidade real da Fábrica, na medida em que a mesma é o resultado da produtividade horária do Posto de Trabalho Gargalo multiplicado pela Eficiência do mesmo - IROG. Ou seja, a medida do IROG é essencial para o cálculo da Capacidade real da Empresa;
• Deixar claro ao trabalhador em seus respectivos Postos de Trabalho as prioridades de Rotina e de Melhorias a serem buscados continuamente no mesmo.
5. Conclusões
Nas Empresas Industriais é muito importante gerir da forma mais eficaz possível os Postos de Trabalho. Para que isto possa ser realizado na prática é necessário compreender de forma ampla os Sistemas Produtivos identificando as principais restrições do mesmo (gargalos, CCRs e Postos com problemas de qualidade) e gerindo estes Postos de Trabalho de forma sistêmica, unificada/integrada e voltada para os resultados. A Metodologia pragmática proposta neste trabalho, utilizando-se essencialmente dos conceitos consagrados em termos da Teoria Das Restrições e do Sistema Toyota de Produção, permite um gerenciamento dos Postos de Trabalho consonante com a obtenção de resultados econômico-financeiros objetivos para as Empresas.
.
6. Referências Bibliográficas
ANTUNES, J. Em Direção a uma Teoria Geral do Processo na Administração da Produção: Uma Discussão Sobre a Possibilidade de Unificação da Teoria das Restrições e da Teoria que Sustenta a Construção de Sistemas de Produção com Estoque Zero, Dissertação de Doutorado no PPGA/UFRGS, Porto Alegre, 1998
GOLDRATT, Eliyahu M., COX, Jeff. A Meta. 12.ed. São Paulo: Educator, 1997
NAKAJIMA, S. Introduction to TPM – Total Productive Maintenance, Cambridge, MA: Productivity Press, 1988.
OHNO, Taiichi. O Sistema Toyota de Produção – Além da Produção em Larga Escala. Porto Alegre: Bookmann, 1997.
SHINGO, Shigeo. O Sistema Toyota de Produção – Do Ponto de Vista da Engenharia de Produção. Porto Alegre: Bookmann, 1996a.
SHINGO, Shigeo. Sistemas de Produção com Estoque Zero: O Sistema Shingo para Melhorias Contínuas. Porto Alegre: Bookmann, 1996b.